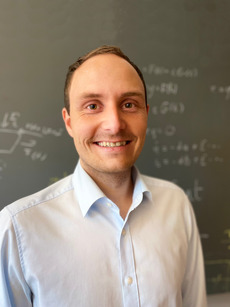
Dr.-Ing. Jens Burgert
- Sprechstunden:
Nach Vereinbarung
- Raum: 206.2
- Tel.: +49 721 608-44150
- jens burgert ∂does-not-exist.kit edu
Institut für Technische Mechanik
Teilinstitut Dynamik/Mechatronik
Geb. 10.23, 2.OG
Kaiserstraße 10
76131 Karlsruhe
Werdegang
03/2016 – 12/2020 | Wissenschaftlicher Mitarbeiter am Institut für Technische Mechanik des KIT Dissertationsschrift: On direct and inverse problems related to longitudinal impact of non-uniform elastic rods Mehrwöchige Forschungsaufenthalte an dem Angström Laboratory, Uppsala, Schweden und an der Technischen Universität Tampere, Finnland |
01/2016 – 02/2016 | Englisch Lehrer AIES International, Vietnam |
04/2013 – 10/2015 | Maschinenbaustudium am Karlsruher Institut für Technologie Vertiefungsrichtung: Theoretischer Maschinenbau Schwerpunkte: Dynamik und Schwingungslehre und Kognitive Technische Systeme Abschluss: Master of Science mit Auszeichnung Masterarbeit: Modellbasierte Entwicklung einer systematischen Vorgehensweise zur Optimierung von elektrischen Antriebssystemen mit veränderlicher Betriebsspannung |
09/2013 – 05/2014 | Auslandsstudium an der Heriot-Watt University Edinburgh, Schottland |
04/2013 – 08/2013 | Werkstudententätigkeit bei der Robert-Bosch GmbH, Bühlertal Aufbau eines parametrischen Hecklappenmodells |
10/2009 – 03/2013 | Maschinenbaustudium am Karlsruher Institut für Technologie Schwerpunkt: Dimensionierung und Validierung mechanischer Konstruktionen Abschluss: Bachelor of Science Bachelorarbeit: Implementierung der thermo-mechanischen Belastung auf eine Kupplungsanpressplatte: Schwerpunkt thermische Berechnung |
10/2012 – 03/2013 | PreMaster bei der Robert-Bosch GmbH, Bühl Geräuschuntersuchung und Modellierung eines elektrischen Kleinmotors |
Spannungswellenoptimierung bei aufeinandertreffenden Stäben
Bei vielen technischen Geräten stoßen Stäbe aufeinander. Beim Schlagbohren, zum Beispiel, wird ein Kolben hydraulisch bzw. pneumatisch beschleunigt und trifft anschließend auf eine Bohrstange. Durch den Stoß zwischen Kolben und Bohrstange wird die kinetische Energie des Kolbens auf die Bohrstange übertragen. Diese leitet die entstehenden Spannungswellen zum Ende der Bohrstange weiter. Dort befindet sich der Bohrbit, mit dem das nachfolgende Material bearbeiten wird.
Trotz der langen Historie des Bohrens sind grundlegende Mechanismen, die zu einem effektiven Bohrprozess beitragen, noch unbekannt. Neuste Untersuchungen zum Thema Optimierung zeigen, dass die Effizienz des Bohrprozesses erhöht werden kann, wenn die in das Gestein einlaufende Spannungswelle ein gewünschtes Spannungsprofil aufweist. Diese Erkenntnis motiviert das Hauptziel des Forschungsvorhabens: Eine Methode zu entwickeln mit der die geometrische Form des Kolbens bestimmt wird, sodass jede beliebig vorgegebene Spannungsform realisiert werden kann. Es handelt sich hierbei um ein inverses Problem, da von der Wirkung (Spannungswelle nach dem Aufprall) auf die Ursache (Geometrie und Auftreffgeschwindigkeit des Kolbens) rückgeschlossen wird. Bei inversen Problemen gilt es außerdem zu klären, ob eine Lösung existiert und ob diese Lösung eindeutig ist.
Zur Validierung der theoretischen Ergebnisse wird ein Prüfstand aufgebaut, mit dem über Dehnmessstreifen (DMS) und mit einem Signalkonditionierer die entstehenden Spannungswellen nach dem Stoß gemessen werden. Mit der Hochgeschwindigkeitskamera lässt sich ermitteln, wann sich der Kolben von der Bohrstange löst. Es lassen sich außerdem interessante Phänomene darstellen. So lässt sich die theoretische Annahme, dass der Stab sich nach dem Aufprall nicht kontinuierlich, sondern in Schüben vorwärtsbewegt (siehe Bild links), validieren.
Contact: Prof. W. Seemann, J. Burgert
Monografien
Burgert, J.
2020, Dezember 15. Karlsruher Institut für Technologie (KIT). doi:10.5445/IR/1000127593
Publikationen
Burgert, J.; Seemann, W.
2019. Proceedings in applied mathematics and mechanics, 19 (1), Articel: e201900007. doi:10.1002/pamm.201900007
Burgert, J.; Seemann, W.
2019. 26th International Congress on Sound and Vibration 2019 (ICSV26), Montreal, Canada, 7 - 11 July 2019, 199–206, Curran
Burgert, J.; Seemann, W.
2018. Proceedings in applied mathematics and mechanics, 18 (1), e201800250. doi:10.1002/pamm.201800250
Burgert, J.; Seemann, W.; Moilanen, C.; Montonen, J.; Miettinen, J.; Saarenrinne, P.
2018. Proceedings of ISMA2018, International Conference on Noise and Vibration Engineering/USD2018, International Conference on Uncertainty in Structural Dynamics : Leuven, Belgium, 17 - 19 September, 2018. Ed.: W. Desmet, 3535–3547, KU Leuven
Burgert, J.; Seemann, W.; Hartenbach, F.
2017. Proceedings in applied mathematics and mechanics, 17 (1, SI), 675–676. doi:10.1002/pamm.201710306
Bearbeiter | Titel | Typ | Datum |
---|---|---|---|
Frederic Cüppers |
Vergleich der Modellierungsansätze bei longitudinalen Stößen in Stäben mit variablem Querschnitt | Bachelorarbeit | 2020 |
Dragos-Corneliu Ana |
Implementierung einer numerischen Methode zur Modellierung von Biegewellen in Balken basierend auf der "Wave Finite Element" Methode | Bachelorarbeit | 2020 |
Aykut Demirkol |
Experimentelle Untersuchung des Einflusses der Kolbengeometrie auf die Wellenausbreitung in aufeinandertreffenden Stangen | Bachelorarbeit | 2019 |
Eric Pihuave |
Experimentelle Untersuchung der Wellenausbreitungsphänomene in unterschiedlichen Materialien | Bachelorarbeit | 2019 |
Betreute Lehrveranstaltungen
WS 21/22 | Mechatronik-Praktikum |
SS 21 | Übungen zu Mathematische Methoden der Schwingungslehre |
SS 20 | Übungen zu Mathematische Methoden der Schwingungslehre |
WS 19/20 | Übungen zu Technische Schwingungslehre |
SS 19 | Übungen zu Mathematische Methoden der Schwingungslehre |
WS 18/19 | Mechatronik-Praktikum |
SS 18 | Übungen zu Experimentelle Dynamik |
SS 18 | Schwingungstechnisches Praktikum |
WS 17/18 | Übungen zu Einführung in die Technische Mechanik II: Dynamik |
SS 17 | Engineering Mechanics IV (Tutorial) |
SS 17 | Übungen zu Technische Mechanik IV |
WS 16/17 | Engineering Mechanics III (Tutorial) |
WS 16/17 | Übungen zu Technische Mechanik III |
SS 2016 | Workshop 'Arbeitstechniken im Maschinenbau' (ITM, Fidlin) |
SS 2016 | Workshop 'Arbeitstechniken im Maschinenbau' (ITM, Seemann) |